FILTER PRESS
Based on application, the high concentrated sludgeflow is pumped into the plate partitioned filter chamber by high pressure diaphragm pump, dewatered by high pressure and process solidified sludge cake and clear filtered water.
NEW……
HIGH PRESSURE FILTER PRESS FROM WATERPOWER High Performance by High Pressure
In a filter press, the moisture content of the wetcake (the solids that stay behind in the chambers during filtration, form a cake which, because is wet in nature has been coined as wetcake) is directly proportional to the Filtration pressure that one can exercise in a given designed unit.
Now with Waterpower’s innovative high pressure filter press design, you need not have to pay a very high premium for getting the ideal results that you required in your filter press.
In a conventional Filter Press, you must be getting 6 to 7 kgs. per square cms. of filtration pressure, which must be resulting in 50% to 75% moisture, depending upon your product and process properties. Now with Waterpower’s HP Filter press, you can get filtration pressure upto 15 kgs. per square cms. and hence, a reduction in moisture content by 50% or more than your present day figures.
Less moisture means:
(1)More Product YIELD per batch.
(2)Less Handling LOSS
(3)Increased product quality (in case of fabric dyes / edible dyes, increased purity)
(4)Ease of handling and substantial SAVINGS on drying costs.
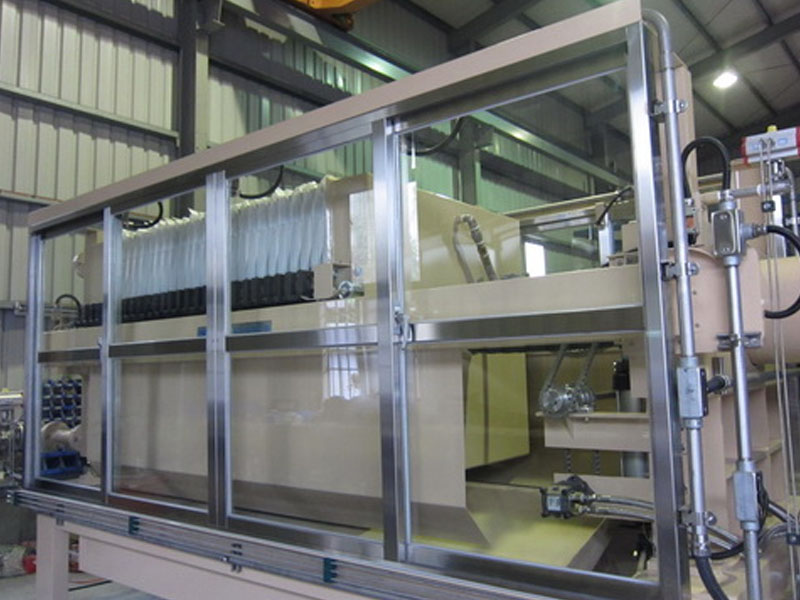
Based on application, the high concentrated sludgeflow is pumped into the plate partitioned filter chamber by high pressure diaphragm pump, dewatered by high pressure and process solidified sludge cake and clear filtered water.
NEW……
HIGH PRESSURE FILTER PRESS FROM WATERPOWER High Performance by High Pressure
In a filter press, the moisture content of the wetcake (the solids that stay behind in the chambers during filtration, form a cake which, because is wet in nature has been coined as wetcake) is directly proportional to the Filtration pressure that one can exercise in a given designed unit.
Now with Waterpower’s innovative high pressure filter press design, you need not have to pay a very high premium for getting the ideal results that you required in your filter press.
In a conventional Filter Press, you must be getting 6 to 7 kgs. per square cms. of filtration pressure, which must be resulting in 50% to 75% moisture, depending upon your product and process properties. Now with Waterpower’s HP Filter press, you can get filtration pressure upto 15 kgs. per square cms. and hence, a reduction in moisture content by 50% or more than your present day figures.
Less moisture means:
(1)More Product YIELD per batch.
(2)Less Handling LOSS
(3)Increased product quality (in case of fabric dyes / edible dyes, increased purity)
(4)Ease of handling and substantial SAVINGS on drying costs.
Filter Press ProcessFilter press operation procedure
Filter Press Out view
※ Our company produces a complete product line of pressure-filtered dryers. According to the properties of the polluted sludge, field space, and customer’s requirements, the most appropriate model can be chosen. The opening methods of filter plates, collection of filtered liquid, sludge cake packaging, auxiliary material dropping system, and types of pressure filtering can also be integrated freely to meet the practical needs.
Application
- Chemical Industries: Medicine, Fertilizer, Dye, Graphite.
- Food Industries:Sugars,Beer,Flour,Soybean Sauce,Beverage Grease, Saccharine,Artificial Flavor etc.
- Mining IndustriesSand and stone pit, Marbles, Mount Morillonite,Bentonite,Calcium Carbonate,Amino Acid,White Smoke etc.
- Metallurgic Industries, Non-iron Metallic Industries.
- Wastewater Treatment and Sludge Denaturing.Filter Press Specification Table
Membrane Filter Press Specification Table
※Other special specifications is accepted